Технологическое оборудование для сборки
В структуре технологических процессов производства изделий машиностроения наибольший удельный вес занимают обработка металлов резанием и сборка. Трудоемкость узловой и общей сборки составляет в среднем около 30 % всей трудоемкости изготовления машин. В массовом и крупносерийном производстве эта доля меньше, а в единичном и мелкосерийном, где выполняется большой объем пригоночных работ, трудоемкость сборки нередко достигает 40 % . Разборка и сборка машин и механизмов в ходе их ремонта в эксплуатационных условиях также является одним из видов сборочных работ. Например, при капремонте трактора ее трудоемкость нередко достигает 70 % трудоемкости при изготовлении. Сборка является одним из наиболее сложных для автоматизации процессов. Это вызвано огромным разнообразием сборочных единиц, узлов, комплексов и т.д. Сборку можно разделить на несколько видов, что позволяет правильно подбирать основное и вспомогательное оборудование (рис. 1) .
Основными организационными формами сборки являются стационарная и подвижная. Первая может выполняться без расчленения и с расчленением сборочных работ на отдельные операции.
Сборку изделий без расчленения сборочных работ выполняют на одном сборочном посту. Все детали и сборочные единицы, необходимые для сборки изделия, поступают на этот пост. Сборку от начала и до конца производит один работающий. При сборке больших изделий работу выполняет бригада. Сборщики должны иметь высокую квалификацию. Этот метод, отличающийся высокой трудоемкостью, применяют только в единичном и опытном производстве Применение специализированного сборочного оборудования практически невозможно. Повышения производительности труда достигают применением механизированного инструмента.
Рис. 1. Классификация сборочных процессов
Более широко применяется сборка с расчленением сборочных операций. В этом случае количество рабочих увеличивается, а общий результат зависит от каждого участника сборочного процесса. Такой техпроцесс состоит из сборки отдельных узлов и общей сборки. При такой организации труда время на сборку сокращается. Дальнейшее расчленение сборочного процесса может привести к тому, что каждый рабочий станет выполнять одну определенную операцию. Осуществить это можно двумя способами — либо перемещением изделия с одного рабочего места на другое, либо перемещением рабочих относительно собираемого изделия. В обоих случаях важно, чтобы относительное перемещение рабочего и изделия было непрерывным. Такая организация сборки характерна для массового и крупносерийного производства и осуществляется с широким применением специального сборочного оборудования . Таким образом, основные различия в видах организации сборки зависят от того, какое это производство — единичное, серийное или массовое.
В целом сборка представляет собой соединение элементов в единое целое с обеспечением заданного техническими условиями качества. Соединения могут быть:
- неподвижные разъемные (резьбовые, пазовые и конические);
- неподвижные неразъемные (соединения запрессовкой или развальцовкой, заклепочные);
- подвижные разъемные (валы — подшипники скольжения, плунжеры — втулки, зубья колес, каретки — станины);
- подвижные неразъемные (некоторые подшипники качения, запорные клапаны)
Уровень механизации и автоматизации сборки определяется по формуле.
где Тм — время механизированных переходов; Тр — затраты времени на все сборочно-разборочные работы; П, П1 — коэффициенты производительности оборудования, характеризующие отношение трудоемкости выполняемых операций на оборудовании с наименьшей производительностью, принятыми за основу, к трудоемкости этих же операций на действующем оборудовании и ручных машинах.
Примерный уровень механизации и автоматизации действующего сборочного производства можно оценить, сравнив с данными табл. 1.
Уровень организации сборочных процессов в зависимости от типа производства, %
Показатель | Уровень | Тип производства | ||
Единичное и мелкосерийное | Серийное | Массовое и крупносерийное | ||
Уровень охвата рабочих механизированным и автоматизированным трудом | Оптимальный | 40…50 | 75 | 85…95 |
Средний | 25…35 | 50. .. 65 | 70…80 | |
Низкий | 10…20 | 40 | До 60 | |
Уровень механизированного (автоматизированного) труда в общих трудозатратах | Оптимальный | 40…50 | 60… 65 | 75…90 |
Средний | 30…40 | 40. ..45 | 60…70 | |
Низкий | 15… 20 | 30 | 50 | |
Уровень охвата сборки поточными методами (без учета единичного производства) | Оптимальный | 20…40 | 70 | 100 |
Средний | 10…20 | 50 | 90 | |
Низкий | До 10 | 30 | 70 |
2. Классификация сборочного оборудования
Оборудование сборочных цехов условно можно разделить на две группы: технологическое, предназначенное непосредственно для выполнения работ по сборке подвижных или неподвижных сопряжений деталей, их регулировке и контролю в процессе узловой и общей сборки, и вспомогательное, назначение которого — механизировать все виды вспомогательных работ, объем которых при сборке изделий весьма большой.
На предприятиях, где уровень механизации невысок, эффективно внедрение на всех этапах сборки электропневмоинструмента, гидравлических ключей и приспособлений, переносных установок с пневмогидроприводом и т. д. На сборке огромен объем вспомогательных и транспортных работ. Например, чтобы выполнить сменную программу по сборке тракторных двигателей Д-240, к сборочным постам надо подать 235 тыс. деталей и комплектующих изделий. Поэтому одновременно с основными работами обязательно надо механизировать и вспомогательные.
В зависимости от возможных масштабов использования сборочное оборудование может быть разделено на универсальное и специальное. Универсальное оборудование применяют в сборочных процессах в мелкосерийном и единичном производстве. В крупносерийном и особенно в массовом производстве оно имеет сравнительно небольшое распространение. Специальное оборудование, как правило, проектируют для выполнения определенной операции с конкретным объектом сборки, поэтому оно может быть использовано лишь на той сборочной единице и той операции, для которой предназначено.
По типу привода сборочное оборудование подразделяют на механическое, гидравлическое, пневматическое и пневмогидравлическое.
В зависимости от назначения оборудование можно разделить на следующие основные группы:
- приспособления-зажимы, которые служат для закрепления собираемых изделий в требующемся для сборки положении;
- установочные приспособления, предназначенные для правильной и точной установки соединяемых деталей относительно друг друга;
- рабочие приспособления, используемые при выполнении операций технологического процесса сборки;
- контрольные приспособления
Сборка крупных сборочных единиц и изделий, например самолетов, кораблей и т д , может выполняться в приспособлениях, называемых стапелями (рис. 2). Они фактически являются приспособлениями-зажимами, удерживающими отдельные узлы во время сборки в нужном положении.
Рис. 2. Сборка самолета на стапеле
Основные требования к сборочному приспособлению состоят в том, чтобы оно обеспечивало точность установки деталей, удобство расположения собираемого объекта, простоту его закрепления, возможность легкого снятия изделия после сборки и безопасность в работе
3. Зажимные сборочные приспособления
На сборочных участках распространенным видом универсальных зажимных приспособлений являются тиски. Преимущество их в том, что они в ряде случаев делают излишним изготовление специальных зажимных приспособлений, особенно если используются сменные губки, форма которых соответствует форме зажимаемой детали. Губки изготовляют из мягкой стали, латуни, меди, алюминия, отливают из свинца. Лучше всего применять быстродействующие тиски с пневматическим приводом (рис. 3). К универсальным зажимным приспособлениям относятся винтовые, эксцентриковые и пневматические струбцины. В зажимных приспособлениях в качестве энергоносителя также используется вакуум.
Тиски с тянущим зажимом (рис. 3, а) имеют усилитель в виде рычага 4. Губка 5 неподвижна, губка 7 перемещается вместе с ползуном 6, на котором она предварительно переустанавливается на шпонке на размер обрабатываемой детали и закрепляется винтом 8. Когда воздух подается через штуцер 1, диафрагма пневмокамеры через шток 3 нажимает на рычаг 4, смещая влево ползун 6 с установленной на нем зажимной губкой При прекращении подачи воздуха в пневмокамеру пружины 2 смещают ползун 5 в исходное положение вправо. Шток 3 при этом опускается. Данные тиски рационально применять в серийном производстве. Тиски, показанные на рис. 3, б, можно применять и в единичном производстве.
Для закрепления детали определенной формы предназначены специальные зажимные приспособления. Они особенно широко применяются в крупносерийном и массовом производстве, бывают стационарными и передвижными и устанавливаются на верстаке или на полу Привод обычно механизированный, чаще всего пневматический (рис. 4). Многие приспособления допускают поворот собираемого изделия в горизонтальной или вертикальной плоскости.
Рис. 3. Зажимные приспособления: а — схема пневматических тисков с тянущим зажимом; б — тиски слесарные цилиндрические с пневмоприводом ТСЦП-180
Рис. 4. Простейшее специальное приспособление пневмозажимом: 1 — пневмоцилиндр одностороннего действия; 2 — основание; 3 — планка прижимная; 4 — стойка; 5 — ось; 6 — опорная призма; 7 — закрепляемая деталь.
При конвейерной сборке зажимные приспособления устанавливают на тележках или пластинах конвейера, а при сборке мелких узлов нередко используют приспособления-спутники, которые вместе с узлом сборщик снимает для выполнения операции на верстаке, а затем опять возвращает на конвейер. Зажимные элементы в таких приспособлениях механические.
Экономическую обоснованность использования приспособления, особенно специального назначения, надо рассчитывать. В общем случае, если в год на данной операции должно собираться А сборочных единиц, а стоимость приспособлений П, то
где К — коэффициент учета расходов на обслуживание приспособления; Зэ — экономия заработной платы, руб. ; Н — цеховые расходы на зарплату сборщиков, %. При сроке амортизации приспособления В лет и сумме годовых расходов на его обслуживание и ремонт в процентах от первоначальной стоимости Р
4. Оборудование для пригоночных и доделочныхработ
Обеспечение полной взаимозаменяемости при сборке изделий экономически оправдано в массовом производстве. В остальных широкое применение при сборке находят пригоночные и доделочные работы. Поэтому различают подготовительные и собственно сборочные операции.
В серийном производстве пригонка нужна для компенсирования неблагоприятного суммирования допусков в многозвенных размерных цепях, а при наличии конструктивных особенностей сопрягаемых деталей пригонка применяется и в крупносерийном, и в массовом производстве. Так, при сборке крупных кузнечнопрессовых машин от 30 до 50 % общей трудоемкости сборки составляют различные доделочные операции.
Наиболее распространенными видами пригоночных работ являются опиливание, зачистка, притирка, полирование, шабрение, сверление отверстий по месту, развертывание отверстий, цекова- ние и гибка. В зависимости от типа производства применяют различные оборудование и механизмы для выполнения этих работ.
Пригоночные работы при сборке механизируют главным образом с помощью универсальных и специализированных инструментов с электрическим, пневматическим, реже с гидравлическим приводом. Пневматическими приводами инструментов служат лопастные и турбинные двигатели. Электроинструменты имеют двигатели переменного тока, коллекторные или асинхронные, питаемые током нормальной или повышенной частоты.
Основные преимущества пневмоинструментов по сравнению с электроинструментами заключаются в большей мощности на 1 кг массы, удобстве и безопасности в применении, бесступенчатом изменении частоты вращения и реверсивном переключении, меньших стоимости и затратах при обслуживании. Однако электроинструменты имеют более высокий КПД, создают меньший шум при работе, легко присоединяются к источнику питания, более транспортабельны.
Для механизации работ по опиливанию и зачистке широко используются угловые шлифовальные машинки-«болгарки», а также шлифмашинки, в шпиндель которых вставляются специальные напильники или абразивные головки (рис. 5) .
Для пригонки плоскостей применяют пневматические шлифовальные машинки, имеющие механизм точной подачи круга по мере его износа. Машинка своей опорной плитой базируется на обработанной поверхности. Величина подачи шлифовального круга может регулироваться в пределах нескольких микрометров.
Рис. 5. Электрическая опиловочно-шлифовальная машина и инструмент к ней: а — общий вид; б — напильники, в — абразивные головки; г — фрезы-шарошки.
Зачистку в труднодоступных местах производят с помощью пневматической турбинной машинки.
В станкостроении для притирки плоскостей применяют механизированные притирочные плиты с гидроприводом. Смонтированные в такой плите двухштоковые гидросистемы со взаимно перпендикулярными осями и некратными рабочими ходами вызывают хаотическое движение притирочной плиты по притираемой поверхности, чем обусловливается высокое качество притирки. Плита подвешивается на балансире.
Для ручной притирки отверстий и наружных цилиндрических поверхностей применяют электрические или пневматические ручные машины с вращательным движением рабочего органа, а также специальные станки. В некоторых случаях притирку выполняют ручными притирами, аналогичными показанному на рис. 6. Притир, чтобы он удерживал абразив (шаржировался), изготавливается из материала более мягкого, чем обрабатываемая деталь: чугуна, стали, латуни, меди, фибры, кожи, фетра, дерева, пластика, стекла и т. д. В качестве абразива проще всего использовать шлифпорошки и пасту ГОИ. Во всех случаях притирам или притираемым деталям сообщается такое движение, чтобы следы не накладывались друг на друга.
Рис. 6. Ручной притир для цилиндрических отверстий: 1 — шайба; 2 — регулировочный винт; 3 — конус; 4 — притир; 5 — вороток.
Одна из конструкций притирочных головок показана на рис 7 7 Принцип ее работы состоит в том, что с помощью двух зубчатых секторов 4, 6 и кулачков 5, 7, установленных на одном валу, притиру сообщаются попеременное возвратно-вращательное движение на определенный угол и периодические подъемы над притираемой поверхностью.
Рис. 7. Головка для притирки седел клапанов, вентилей и подобных деталей: 1 — стол станка; 2 — деталь; 3 — притир; 4, 6 — зубчатые секторы; 5, 7 — кулачки; 8 — шпиндель станка; 9 — пиноль.
Применение таких головок повышает производительность в 5 раз и более по сравнению с ручной притиркой.
Шабрение сопрягаемых, чаще всего трущихся поверхностей — процесс трудоемкий. Например, при ремонте некоторых станков на долю шабрения приходится до 40 % трудоемкости всех слесарных работ. Там, где можно, шабрение надо заменить другими более производительными способами обработки. Например, шабрение охватывающих цилиндрических поверхностей заменяется развертыванием, растачиванием и протягиванием. Шабрение плоскостей корпусов редукторов, плитовин рабочих клетей прокатных станов, станин, ползунов, направляющих планок и других деталей заменяют тонким строганием и шлифованием.
Для механизации шабрения применяют специальные инструменты и шабровочные установки. Один из таких инструментов — механический шабер со встроенным в корпус асинхронным электродвигателем мощностью 90 Вт, работающим от трехфазного тока 36 В, 200 Гц, — показан на рис. 8. Длина хода ножа-пластинки 1 до 20 мм, частота — 1200 двойных ходов в минуту. По такой же схеме устроены широко применяемые шаберы с пневматическим двигателем. Часто в качестве привода перемещения пластины шабера используется кривошипный механизм При шабрении больших поверхностей применяют шабровочные станки. Электромеханический шабер с гибким валом (рис. 9) состоит из электродвигателя 8, смонтированного с тележкой 5 и подвешенного на монорельсе 4 Электродвигатель передает движение редуктору 7, с которым соединен гибкий вал 6, приводящий в движение кривошип 3, сообщающий возвратно-поступательное движение штоку 2.
Рис. 8. Электрическая шабровочная машинка: 1 — пластина шабера; 2 — плунжер; 3 — шаровая опора; 4 — рамка плунжера; 5 — ось рамки; 6 — рамка ворота; 7 — ось привода рамки плунжера; 8 — выходной вал редуктора; 9 — корпус электродвигателя и редуктора.
Рис. 9. Электромеханический шабер: 1 — пластинка; 2 — шток; 3 — кривошип; 4 — монорельс; 5 — тележка; 6 — гибкий вал; 7 — редуктор; 8 — приводной электродвигатель.
При шабрении мелких деталей и сборочных единиц для их закрепления целесообразно пользоваться электромагнитными плитами
5. Оборудование для сверлильных работ
Весьма часто при выполнении сборочных работ требуется сверлить отверстия по месту. Сборочные цеха для таких операций обычно имеют несколько сверлильных станков, установленных вблизи линии сборки. Для отверстий диаметром до 10. . .12 мм применяют переносные приспособления или небольшие станки на колонках, а для более крупных — станки на фундаменте.
На рис. 10 показана переносная сверлильная машина МС-1 для сверления и развертывания отверстий при сборке. Сверлильная машина своим магнитным основанием устанавливается на станине собираемого изделия. Сила притяжения основания 9500 Н. Размер машины 187 х 240 х 376 мм, масса 10,5 кг.
Рис. 10. Сверлильная машина МС-1 ЗАО НПО «Вектор» (г. Гродно)
Питается она напряжением 220 В и позволяет с помощью кольцевого сверла обрабатывать отверстия диаметром до 40 мм. Для перемещения сверлильной головки имеются трубчатые цилиндрические направляющие, СОЖ подается в зону резания.
Другие модификации этой машины могут обработать отверстия диаметром до 130 мм и глубиной до 200 мм с помощью кольцевого сверла, а также работать спиральным сверлом, нарезать резьбу до М30, разворачивать отверстия диаметром до 32 мм, имеют приспособления для закрепления на цилиндрических заготовках, поворотный относительно магнитного основания корпус, привод с бесступенчатым регулированием частоты вращения инструмента.
На сборке отверстия сверлят пневматическими машинами различных конструкций. При сборке узлов и панелей крупных изделий на стапелях возникает необходимость совместного сверления и развертывания большого количества отверстий (до 40 000 на машину). Использование обычных пневматических сверлильных машин с последующим развертыванием отверстий увеличивает трудоемкость сборочных работ. Для механизации обработки в таком случае можно применить специальный сверлильный пневматический агрегат СПА-20. Он имеет два ротационных двигателя: для привода шпинделя мощностью 0,75 кВт и для подачи мощностью 0,34 кВт. Число оборотов шпинделя регулируется от 100 до 800 в минуту, подача — от 0 до 250 мм/мин. При работе агрегат подвешивают на специальную подвеску с балансиром, что позволяет перемещать его в двух направлениях Сверление, зенкерование и развертывание отверстий производится по накладной кондукторной плите.
6. Оборудование для полирования
Полирование при сборке производят для достижения меньшей шероховатости и улучшения товарного вида изделия. Основное отличие полирования от зачистки заключается в том, что применяются не абразивные круги, а круги из войлока, хлопчатобумажной ткани, специальной бумаги. Применяемый инструмент определяет и конструкцию станков. По большей части это круглошлифовальные станки для наружного центрового и бесцентрового шлифования или обдирочно-шлифовальные станки и некоторые другие конструкции. Отдельную группу представляют станки, работающие с применением химического действия электрического тока. На рис. 11, а показан полировальный станок, станина 14 которого установлена на тумбе 16. В верхней части станины размещены полировальные бабки, а в нижней — фланцевые двухскоростные электродвигатели 5 и 8. В станине смонтированы клиноременные вариаторы с выходной частотой вращения от 1000 до 4000 мин -1 и пульт управления 6. Механизм для измерения частоты вращения шпинделя состоит из тахометра 7 и двух валиков с резиновыми дисками, закрепленными на внутренних концах шпинделей. На шпинделе 4 закреплен полировальный круг 1, который огражден кожухом 2 с подручником 3. На шпинделе 9 установлен контактный ролик 10 для абразивной ленты. Лента ограждена кожухом 11 с подручником 15, ее натяжение регулируется механизмом 12
Для полирования применяют ручные электрические угловые и обыкновенные полировальные машинки. Они имеют регулируемый привод, а некоторые — возможность контролировать частоту вращения круга. Кроме электрических, применяют шлифовальные машинки с пневматическим приводом аналогичные тем, что используются для зачистки.
Рис. 11. Универсальный полировальный станок ВТМ250: а — схема; б — общий вид
7. Сборочное оборудование для гибочных работ
Гибочные работы на сборке выполняются для подгонки труб и изготовления кожухов. Гибка труб может быть и основной операцией при изготовлении мебели и подобных работах. По степени механизации трубогибные станки делятся на три класса:
- трубогибы с ручным управлением;
- полуавтоматические трубогибочные станки;
- автоматические трубогибы.
Простейшим устройством для гибки труб обкаткой роликом (рис. 12) являются ручные трубогибы, которыми пользуются при малом объеме гибки труб одинакового диаметра. При больших объемах механизацию гибки осуществляют с помощью гидравлических или пневматических прессов методом штамповки.
Рис. 12. Гибка обкаткой: а — профильным роликом; б — прямым роликом с помощью профильной накладки.
Трубогибочный станок С-288 (рис. 13) с электромеханическим приводом предназначен для холодной гибки труб диаметром от 1″ до 3″ способом наматывания. Он состоит из корпуса 1 с механизмами.
приводного и главного валов, поворотного стола 2 с гибочным роликом, рамы 6, тяги с дорном, суппорта 3 со сменной планкой. Гибочный ролик, зажим и ползун сменные и выбираются в зависимости от диаметра изгибаемой трубы.
Рис. 13. Общий вид трубогибочного станка С-288
Рис. 14. Кинематическая схема трубогибочного станка С-288
Включение станка производится вручную при помощи рукоятки 4, а выключение — при помощи передвижного упора, укрепленного на поворотном столе 2. Упор переставляется в зависимости от нужного угла загиба.
Кинематическая схема трубогибочного станка показана на рис. 14. Привод поворотного стола 6 осуществляется от электродвигателя 1 при помощи клиноременной передачи 8- 7, вращающей главный вал через червячную передачу 2-3. Установленное на главном валу червячное колесо 3 через зубчатую муфту 4 вращает зубчатое колесо 5, поворачивающее стол 6. Зубчатая муфта 4 включается с помощью рычага вручную, и тогда зубчатое колесо 5 вращает поворотный стол с установленным на нем гибочным роликом.
Гибочный ролик крепится к поворотному столу при помощи гайки с быстросъемной шайбой, что позволяет быстро заменять его без полного свинчивания гайки с оси поворотного стола.
Труба на станок устанавливается вручную. Выключается станок по окончании гибки автоматически при помощи конечного выключателя или вручную посредством рукоятки.
Станок для гибки труб с нагревом токами высокой частоты (рис. 15) предназначен для гибки труб наружным диаметром от 95 до 300 мм. Станок состоит из сварной станины 1, на которой расположены каретка 6 для закрепления трубы, механизм продольной подачи 2, каретка 10 направляющих роликов 7, каретка 12 нажимного ролика 11, а также индуктор 9 для индукционного нагрева трубы. Каретка закрепления трубы перемещается вдоль станины при помощи ходового винта продольной подачи. Закрепляется труба на каретке 6 при помощи двух губок 5, одна из которых подвижна. Подвижная губка перемещается при помощи рукоятки 20 вручную и прижимает трубу к неподвижной губке. Ось изгибаемой трубы 4 эксцентрична по отношению к станине (величина эксцентриситета различна для труб разного диаметра)
Рис. 15. Станок для гибки труб с нагревом токами высокой частоты: 1 — станина; 2 — механизм продольной подачи; 3 — удлинитель; 4 — изгибаемая труба; 5 — губки; 6, 10 — каретки; 7 — направляющие ролики; 8 — держатель индуктора; 9 — индуктор; 11 — нажимной ролик; 12 — каретка нажимного ролика; 13 — винт поперечной подачи; 14 — механизм поперечной подачи; 15 — конечный выключатель; 16 — система охлаждения; 17 — ходовой винт; 18, 20 — рукоятки; 19 — ролик.
Каретка 10 направляющих роликов 7 служит для направления движения трубы при гибке и для восприятия изгибающего усилия. Она перемещается ходовыми винтами, связанными между собой конической передачей. Один из направляющих роликов 7 укреплен на ползуне и может перемещаться вручную винтом 17. Оба ролика 7 свободно вращаются на своих осях. На каретке направляющих роликов закреплены держатель 8 индуктора 9, высокочастотный трансформатор (на рисунке не показан) и элементы системы охлаждения 16.
Каретка 12 нажимного ролика 11 закреплена неподвижно. По основанию каретки перемещается ползун с запрессованной осью, на которой и вращается нажимной ролик 11. Перемещение ползуна осуществляется с помощью ходового винта 13, приводимого в движение механизмом поперечной подачи 14. На каретке нажимного ролика установлены два конечных выключателя 15 для ограничения хода нажимного ролика в зависимости от выбранного радиуса гибки. Сменный индуктор 9 для нагрева труб представляет собой кольцо из медной трубки, которое охлаждается водой, подводимой по шлангу.
Для дополнительной поддержки снизу изгибаемой трубы на станке установлен ролик 19, который перемещается с помощью рукоятки 18 в зависимости от длины трубы. При гибке очень длинных труб к каретке зажима присоединяют специальные удлинители 3, которые поддерживают свисающую часть трубы.
Рис. 16. Трубогиб с ЧПУ ERCOLINA TB130 фирмы CML International S. p. A. (Италия) для бездорновой гибки труб
Сейчас широко распространены тру- богибы с ЧПУ для бездорновой гибки труб (рис. 16). (Дорн — это извлекаемая вставка в трубу, предотвращающая ее смятие и гофры. ) Они обеспечивают изгибание труб различных диаметров и толщины стенки. Максимальный угол гиба достигает 180°. В зависимости от наружного диаметра трубы, ее материала и толщины стенки станки обеспечивают радиус гиба от 36 до 700 мм (по оси трубы) с учетом упругой отдачи ЧПУ обеспечивает контроль по осям С и Х и возможность получения пространственной фигуры. Конструкция станка обеспечивает его быструю переналадку для обработки новых заготовок.
Для гибки кромок и разных профилей в одной или нескольких плоскостях под разными углами применяют листогибочные прессы (рис. 17) . Гибка профилей осуществляется пуансоном 2 (рис. 17, б), закрепленным на раме ползуна 1 на матрице 3, которая устанавливается на подкладке 4 плиты 5 пресса или непосредственно на плите. Пуансоны различаются по форме и радиусам гибки. Рабочая часть матрицы представляет собой гнездо, выполненное обычно в форме угольника, прямого или радиусного паза. Некоторые из применяемых для гибки различных профилей пуансонов и матриц показаны на рис. 17, в.
Для гибки профилей различных сечений используют роликовые гибочные станки с тремя или четырьмя роликами.
Рис. 17. Листогибочный пресс: а — общий вид; б — рабочая зона; в — формы изгибаемого профиля; 1 — рама ползуна; 2 — пуансон; 3 — матрица; 4 — подкладка; 5 — плита
8. Оборудование для сборки неподвижных разъемных соединений
Постановка шпилек с помощью ручных инструментов — малопроизводительная и трудоемкая операция; поэтому там, где возможно, надо использовать механизированный способ, т. е. применять шпильковерты, а лучше специальные стационарные установки. Шпильковерт является слесарно-сборочным инструментом и отличается от гайковерта только наличием специальной головки для удерживания шпилек при их завинчивании.
Рис. 18. Общий вид полуавтомата для заворачивания десяти шпилек
В полуавтомате (рис. 18) для завинчивания десяти шпилек применена гидравлическая самодействующая силовая головка с двумя электродвигателями: 1 — для привода шпинделя, 2 — для привода гидронасоса. Привод от электродвигателя 1 передается к 10-шпиндельной головке 3. После включения пусковой кнопки силовая головка быстро опускается вниз. Когда шпиндели 4 подходят на расстояние 5. . .10 мм к шпилькам, включается рабочая подача, и патроны вначале навинчиваются на шпильки, а затем последние завинчиваются в блок Об окончании процесса завинчивания свидетельствует срабатывание тарированных муфт шпинделей, при этом патроны доходят до упора и через реле давления включается реверс Патроны свинчиваются со шпилек, а силовая головка быстро возвращается в исходное положение. Продолжительность цикла примерно 45 с.
Резьбовое соединение болта с гайкой выполняется на вертикально-сверлильном станке с приспособлением 1 (рис. 19, а). Предварительно собранные с болтом 4 детали 2 и 3 ставятся в приспособление 1. На шпинделе 7 закреплена специальная головка с гайками. При ее сближении с болтом 4 гайка 6 наворачивается на болт до тех пор, пока не попадет в фаску 5 и не выйдет из зацепления с головкой После этого вращение гайки прекращается.
Для достижения высокого качества сборки болтовых соединений из-за опасности смятия первого витка, срыва резьбы и заедания важным является правильное наживление гайки При механическом наживлении гайка должна иметь как можно больше степеней.
Рис. 19. Сборка болта с гайкой: а — приспособление; б — головка для наживления гаек.
свободы. Для обеспечения этого применяют специальные головки (рис. 19, б), в которых гайка удерживается подпружиненными шариками и самоустанавливается относительно болта (шпильки) . Головку можно установить на ручной пневматический или электрический гайковерт или на вертикально-сверлильный станок.
Для качественной сборки резьбового соединения (обеспечения требуемого момента затяжки) в конструкции гайко- и винтозавертывающей машины важны конструктивные особенности приводного двигателя и муфты, с помощью которой крутящий момент от двигателя передается на шпиндель. Такие муфты бывают:
- прямого привода (полностью передают создаваемый двигателем крутящий момент на шпиндель при невысокой точности затяжки);
- ударно-импульсными (передают крутящий момент с помощью ударов — создают большой, но неточный по величине крутящий момент);
- ограничительными (передают шпинделю крутящий момент определенной регулируемой с повышенной точностью величины);
- предельными (отключают двигатель при достижении нужной величины затяжки соединения — обеспечивают повышенную точность)
Гайковерты могут быть пневматическими, гидравлическими и электромеханическими.
Для навинчивания гаек с резьбой большого диаметра используются пневматические поршневые гайковерты, способные развивать крутящий момент до 10 000 Н • м. Затяжку резьбовых соединений можно выполнять с помощью рычажных механизмов, закрепляемых на собираемом узле. В этом случае ключ с плечом 1 м поворачивается с помощью гидроцилиндра. С помощью такого механизма можно создать крутящий момент 100 000 Н • м. Хорошие результаты по обеспечению заданного крутящего момента (±5 %) дает применение в гайковертах устройств обратной связи, отключающих приводной двигатель.
Несмотря на то что при сборке резьбовых соединений с большими крутящими моментами в подавляющем большинстве случаев применяют одношпиндельные заворачивающие устройства, предпочтение надо отдавать многошпиндельным. Показанный на рис. 20 гайковерт, используемый на Калининской АЭС, позволяет заворачивать одновременно 54 шпильки, существенно повышая производительность.
Рис. 20. Гайковерт для заворачивания 54 шпилек
Для заворачивания винтов с диаметром резьбы до М30 мм в мелкосерийном производстве применяется приспособление, аналогичное приведенному на рис. 21. Узел 1 помещают на поворотном столе 10 установки. Повернуть его можно штурвалом 11. Коробка передач 5 со шпинделем 4 имеет возможность перемещаться при вращении маховика 6 в вертикальном направлении. Шпиндель 4 имеет на конце торцовый ключ 9. Так как конечное зубчатое колесо 3 имеет возможность свободно поворачиваться с помощью маховика 7 на шлицевой втулке на угол 120°, ключ 9 может быть легко установлен на винт 2 при любом положении граней его головки. Реле максимального тока, отрегулированное на определенный крутящий момент на шпинделе 4, автоматически отключает электродвигатель 8, когда момент затяжки винтов достигнет такого значения Установку можно переналаживать для выполнения сборочных работ на различных сборочных единицах.
Обеспечение правильной затяжки резьбовых соединений позволяет снизить запасы прочности и массу изделий. Затяжка обеспечивается конструкцией ключей, которые могут быть двух типов:
- предельные (автоматически выключаются при достижении нужного момента затяжки);
- динамометрические (указывают создаваемый при затяжке момент)
Рис. 21. Схема приспособления для заворачивания крупных болтов
В особо ответственных случаях затяжка болтов и шпилек может выполняться за счет предварительного растягивания стержня болта или шпильки в пределах упругой деформации на нужную длину со свободным заворачиванием гайки. Для этого может использоваться гидравлическая установка с приспособлением, показанным на рис. 22.
Рис. 22. Схема приспособления для растягивания болтов для затяжки резьбового соединения
Корпус приспособления 5 опирается на собираемую сборочную единицу 1. При этом головка 4 навинчивается на выступающий конец болта (шпильки) 3. После этого под поршень 7 подается масло под давлением, обеспечивающим заранее рассчитанную силу растяжения болта (шпильки) 3 в пределах упругой деформации. Поршень через шток 6 и головку 4 растягивает болт. Гайка 2 при этом освобождается и через окно в корпусе приспособления 5 легко заворачивается до контакта с собираемыми деталями. Давление на поршень 7 снимается, и болт 3, укорачиваясь, создает необходимое усилие затяжки резьбового соединения, а приспособление демонтируется. Неравномерность затяжки, полученной данным способом, колеблется от 5 до 7 %.
9. Оборудование для сборки конических соединений
Сборка конических соединений технически проще сборки цилиндрических из-за самоцентрируемости втулки и вала Нужная величина натяга достигается с помощью гидравлических прессов, которые обеспечивают прикладывание усилия к валу или втулке. Кроме прессов, можно применять домкраты или специальное приспособление, называемое гидравлической гайкой. В конических соединениях небольших размеров сила запрессовки чаще всего создается обыкновенной гайкой Нормальные результаты получают нагревом до расчетной температуры конической втулки или адекватным охлаждением конического вала.
10. Оборудование для сборки неподвижных неразъемных соединений
Существует множество разновидностей неподвижных неразъемных соединений. В целом их можно разбить на три группы:
- соединение за счет пластических деформаций;
- герметичное соединение за счет соответствующей формы;
- соединение за счет молекулярных сил.
Рассмотрим оборудование для соединения за счет пластических деформаций и клепки.
Соединения за счет пластических деформаций условно делят на поперечно-прессовые и продольно-прессовые.
В поперечно-прессовых соединениях сближение сопрягаемых поверхностей происходит за счет увеличения или уменьшения диаметра соединяемых деталей. Такие соединения осуществляют нагреванием охватывающей детали перед сборкой, охлаждением охватываемой детали, пластической деформацией (например, развальцовкой), приданием упругости охватываемой детали.
При продольно-прессовом соединении охватываемая деталь под действием прикладываемых вдоль оси сил запрессовывается в охватываемую.
Нагрев охватываемой детали в зависимости от ее конструкции и назначения производят в газовых или электрических печах в воздушной или жидкостной среде. При необходимости выдерживания точной температуры нагрев производят в жидкости. Для этого используют металлический бак с тепловой изоляцией, снабженный электронагревательными элементами. В бак заливается минеральное масло и с помощью пневмоцилиндров, электропривода или электротельфера вставляется сетчатая металлическая корзина с нагреваемыми деталями По истечении нужного времени корзина приподнимается над баком, масло стекает и детали извлекаются из корзины для сборки.
Зубчатые колеса хорошо нагревать токами высокой частоты в индукторе, охватывающем одно зубчатое колесо или их стопку Для нагрева втулок можно использовать электрическую спираль, выполненную по диаметру отверстия детали. Мощность спирали может составлять десятки киловатт.
Охлаждение охватываемой детали по сравнению с нагревом не вызывает внутренних напряжений и местных деформаций Для охлаждения нужно меньше времени, и можно на один охлажденный вал установить одновременно несколько охватывающих деталей. Да и прочность соединения выше, чем при нагреве, на 10. . .15 %.
Для охлаждения до -75 °С используют твердую углекислоту, которой наполняют деревянный или металлический ящик с деталями. Ящик должен иметь хорошую теплоизоляцию. Для охлаждения до -100 °С и ниже применяют жидкий воздух, кислород или азот. При этом можно использовать установку, аналогичную показанной на рис. 23.
Камера для охлаждения жидким газом представляет собой деревянный ящик 2, усиленный металлической обшивкой Жидкий газ из сосуда 8 поступает в змеевик 3, расположенный внутри усиленной теплоизоляции 4. Охлаждаемая деталь 5 помещается внутри змеевика 3.
Современные установки глубокого охлаждения снабжены системами электронного управления, которые поддерживают температуру с точностью до ±0,5 °С.
При сборке неподвижных неразъемных соединений часто применяют прием вальцевания, когда охватываемую деталь раскатывают, увеличивая в размере, а охватывающую обкатывают, уменьшая.
Рис. 23. Общий вид установки для охлаждения деталей жидким газом: 1 — испаритель; 2 — деревянный ящик; 3 — змеевик с жидким газом; 4 — теплоизоляция; 5 — заготовка; 6 — трубка подачи жидкого газа; 7 — кожух; 8 — сосуд с жидким газом.
Такое соединение обеспечивает герметичность, но разборка его затруднительна и ведет к порче деталей. Выполняют данный вид сборочной операции на вертикально-сверлильном станке или приспособлением, обеспечивающим вращение инструмента, называемого вальцовкой. Одним из примеров данной операции является развальцовка на конус трубок малого диаметра для выполнения герметичных соединений трубопроводов. Способом раскатки можно установить тонкостенную втулку в корпусе.
Радиальное обжатие втулкой шланга на штуцере выполняют на гидравлическом или пневматическом прессе в приспособлении с 4-6 ползунами.
От 10 до 12 % сборочных работ могут занимать операции выполнения продольно-прессовых соединений: запрессовка валов в зубчатые колеса, втулки, напрессовка колец подшипников и т.п. Выполняются они с помощью прессов различных конструкций Величина усилия запрессовки (характеристика пресса) рассчитывается по известным формулам с учетом коэффициента запаса усилия от 1,5 до 2. Усилие распрессовки прессовых соединений с натягом больше, чем при сборке, на 10. . .15 %. Поскольку прессы являются широко распространенным сборочным оборудованием, то надо отметить, что их конструкции весьма разнообразны (рис. 24), выбирают их исходя из конкретных условий производства.
Рис. 24. Виды сборочных прессов
Среди названных прессов на сборке широко распространены прессы, действующие от сжатого воздуха, поступающего из цеховой магистрали. Для увеличения силы запрессовки применяют рычажные пневмопрессы (рис. 25). В конструкции пресса можно применять нормализованные пневмоцилиндры диаметром 150, 200, 250 и 300 мм для сил на штоке цилиндра при давлении воздуха 0,5 МПа, соответственно, 700, 12 250, 19 200 и 27 730 Н.
Рис. 25. Схема пневмопресса с рычажным усилением: 1 — основание;2 — рабочий плунжер; 3 — рычаг; 4 — пневмоцилиндр.
Для еще большего увеличения силы применяют пневмопрессы со сдвоенными цилиндрами, а когда надо создать при запрессовке усилие 200 1000 кН, а то и больше, применяют гидравлические или пневмогидравлические прессы. В гидропрессе основными узлами являются насосная установка с электродвигателем, рабочий цилиндр с поршнем и штоком, электрогидравлическая панель с реверсивным золотником и система управления (ножная или ручная).
В насосной установке для нагнетания масла под давлением обычно используют лопастные насосы. При двух спаренных насосах разной производительности путем комбинации их включения в сеть достигаются три ступени хода пресса . Необходимая последовательность включения на многих прессах обеспечивается автоматически, вследствие чего создается рациональный цикл работы. Пульсирующая подача масла в гидроцилиндр уменьшает силы запрессовки. Поэтому гидропрессы иногда снабжают специальными гидровибраторами.
На сборке небольших сборочных единиц в мелкосерийном производстве применяют разнообразные ручные прессы. Они недороги, просты в эксплуатации, но малопроизводительны и требуют больших затрат труда. В условиях массовой сборки небольших сборочных единиц рациональны полуавтоматические механические прессы (рис. 26). Поворотный стол 2 совершает вращательное движение. Детали собираемых сборочных единиц устанавливают в приспособления 5 на поворотном столе. Запрессовка происходит, когда рабочий плунжер 3 набегает на скос кулачка 4. При дальнейшем повороте стола кулачок выталкивателя 7 поднимает выталкиватель 6 и собранный узел сбрасывается в лоток. Такие прессы обладают высокой производительностью — до 3000 узлов в час.
11. Оборудование для выполнения заклепочных швов
Для создания неразъемного соединения в машиностроении находят применение заклепочные швы. В зависимости от назначения сборочной единицы, ее конструкции, размеров применяемых заклепок и типа производства клепку осуществляют на прессах, с помощью специализированных приспособлений или посредством механизированного инструмента.
Рис. 26. Схема полуавтоматического пресса: 1 — коробка скоростей; 2 — поворотный стол; 3 — рабочий плунжер; 4 — кулачок; 5 — установочное приспособление; 6 — выталкиватель; 7 — кулачок выталкивателя.
Заклепочные соединения можно собирать электромеханическими прессами, приводимыми в движение электродвигателем, пневматическими прессами рычажного и прямого действия (см. рис. 25), пневмогидравлическими прессами с гидравлическим мультипликатором, гидравлическими прессами прямого действия и механическими клепальными машинами. Сила клепки, создаваемая прессами и машинами, колеблется от 20 до 1000 Н, иногда больше. Мощными прессами одновременно расклепывают несколько заклепок.
Малогабаритные сборочные единицы для сборки устанавливают на стационарные прессы или установки, а крупные сборочные единицы собирают, например, переносной клепальной скобой (рис. 27).
Рис. 27. Переносная гидравлическая клепальная скоба: 1 — шток; 2 — корпус скобы; 3 — отверстия подачи масла; 4 — поршни; 5 — отверстие выхода масла; 6 — пуансон верхний; 7 — пуансон нижний.
Клепальная скоба работает от гидростанции, подающей масло под давлением 6 МПа в отверстие 5. Поршни 4 смещаются вниз, и верхний пуансон 6 формирует головку заклепки. При диаметре цилиндра 175 мм развивается усилие около 280 кН, что достаточно для формирования стальной заклепки диаметром до 12 мм. Регулирование подачи масла и скорости деформирования заклепки осуществляется нажатием на кнопку, смонтированную на корпусе скобы 2. Эта скоба — средней мощности. Гидравлические клепальные установки высокой мощности развивают усилие клепки до 800 кН.
Применяют также клепальные машины ударного действия, широко используют клепальные молотки — пневматические и реже электрические. Пневматические молотки могут быть прямые, угловые, бугельные, удлиненные.
В серийном производстве для клепки используются обычные прессы, применяемые при сборке.
На заводах крупносерийного и массового производства во многих случаях для сборки различных узлов используются специальные станки, разработанные под конкретные технологические процессы. Например, автоматические линии сборки поршня с поршневым пальцем и шатуном и установки на поршень компрессионных и маслосъемных колец, станки для притирки клапанов к гнездам в двигателе внутреннего сгорания и т. д.
12. Оборудование для балансировки сборочных единиц и деталей
Неуравновешенность вращающихся механизмов приводит к вибрации, что ухудшает их управляемость, отрицательно влияет на прочность и вредно отражается на здоровье обслуживающего персонала. Балансировку деталей обычно осуществляют в механических цехах при их изготовлении.
Производят статическую и динамическую балансировку сборочных единиц — роторов. Статическую балансировку выполняют аналогично статической балансировке шлифовальных кругов на горизонтальных параллельных направляющих, на роликах, на сферической пяте, на весах и на специальных станках.
Выпускаются универсальные и специальные балансировочные станки для сборочных единиц и изделий массой до 100 т (рис. 28), позволяющие уравновешивать детали и узлы одновременно в двух плоскостях, балансировочные машины резонансного типа, а также полуавтоматическое и автоматическое балансировочное оборудование. Выпускает балансировочные станки и УП «МЗОР» .
Рис. 28. Балансировочный станок с электронной системой управления: а — общий вид; б — схема балансировочного станка с ваттметровым измерительным устройством; 1 — привод; 2 — двухшарнирный вал; 3, 5 — опоры; 4 — балансируемый ротор; 6, 9 — датчики; 7, 8 — оси, проходящие в плоскостях измерения; 10 — переключатель «угол — величина»; 11 — ваттметровый индикатор; А — А, Б — Б — плоскости исправления
13. Оборудование для испытания соединений
Плотные соединения, подвергающиеся в процессе эксплуатации воздействию разности давления гидравлической среды (вода, масло и т. п. ), а также замкнутые системы и резервуары, выдерживающие большие давления, после сборки подвергают гидравлическим испытаниям: в рабочую полость узла под давлением подают жидкость — обычно эмульсию — и контролируют, нет ли течи.
В ряде случаев испытание проводят сжатым воздухом. Испытуемую камеру сборочной единицы также изолируют от окружающей среды заглушками и заполняют воздухом при давлении от 3 до 4,5 МПа. Если это давление сохраняется в камере после перекрытия крана, соединяющего камеру с воздушной магистралью, то результат считается удовлетворительным. Для проверки герметичности стыков, а также заглушек контролируемые соединения покрывают тонким слоем масла, а внутрь подводят сжатый воздух. Если какое-либо соединение недостаточно плотно, происходит утечка воздуха, который в виде пузырьков обнаруживается на покрытой маслом поверхности.
Технологическое оборудование, необходимое для проведения этих испытаний, представляет собой насосную установку для подачи эмульсии под давлением, приспособления для герметизации всех отверстий детали или сборочной единицы и аппаратуру управления. Обычно такое оборудование проектируется под конкретные испытания
14. Устройства для заправки рабочих жидкостей
Многие собранные сборочные единицы заправляют рабочими жидкостями или консистентными смазками. Для этого применяются различные дозаторы. В единичном производстве это чаще всего шприцы и насосы. При небольших объемах заправляемой жидкости в массовом и крупносерийном производстве применяют поршневые дозаторы, аналогичные показанному на рис. 29.
При подаче сжатого воздуха поршень пневмоцилиндра 3 перемещает шток 4 и нагнетательный поршень 5, который через клапан подачи 8 подает рабочую жидкость в трубопровод и в заправляемый узел 9. Обратный клапан пропускает жидкость из основного резервуара в пространство правее нагнетательного поршня 5 самотеком. Количество подаваемой рабочей жидкости регулируется гайкой 1, которая ограничивает ход поршня пневмоцилиндра.
В серийном производстве рациональнее использовать дозаторы с электронным управлением, позволяющие дозировать порции массой от 2 до 1000 кг с точностью ±1 % или ±0,01 л и регулировать температуру рабочей жидкости на выходе из дозатора.
Рис. 29. Схема заправки сборочных единиц рабочей жидкостью: 1 — гайка регулировки объема; 2 — штуцера подачи сжатого воздуха; 3 — поршень пневмоцилиндра; 4 — шток; 5 — нагнетательный поршень; 6 — рабочая жидкость; 7 — обратный клапан; 8 — клапан подачи; 9 — заправляемый узел
15. Моечное оборудование
Перед сборкой или покраской детали и узлы подвергают мойке. Существует много способов мойки, но чаще других применяют следующие:
- химический (мойка окунанием и струйная мойка с применением органических растворителей);
- электрохимический (в спокойном или принудительно возбуждаемом электролите);
- ультразвуковой
Для реализации этих способов создают различные моечные установки и машины. Простейшая моечная машина показана на рис. 30. Корпус 1 — сварной конструкции из листовой стали. В передней его части находится двухстворчатая или подъемная дверка 4, через которую на тележке 2 вкатываются по рельсам изделия 3, подлежащие промывке. Возможен вариант с подвеской тележки на монорельс. Если моечная машина проходного типа, то дверки есть с двух сторон. Снизу, сверху и с боков тележки размещены коллекторы 5 с насадками. Коллекторы соединены трубопроводами с насосом 6, вращаемым электродвигателем. Нижней частью установки является бак. Моющий раствор нагревается в баке с помощью электричества 8 или пара до 80. . .90 °С, откуда насосом 6 подается к коллекторам 5 и, разбрызгиваясь через насадки, промывает изделия, подвешенные на штырях тележки или лежащие на ней. Для промывки мелких деталей используют решетчатую тару После промывки детали продувают сжатым воздухом.
Рис. 30. Схема моечной машины
В массовом производстве для мойки однотипных сборочных единиц, используемых в больших количествах, применяют механизированные установки.
Для очень тщательной очистки процесс мойки проводят при наложении ультразвука, от которого в жидкости образуются кавитационные пузырьки, механически воздействующие на загрязненную поверхность. Лопаясь, они создают ударные волны и интенсивно разрушают слои смазки и грязи. Высокочастотные колебания в обычной моечной машине создаются пьезокварцевым или магнитострикционным преобразователем. Жидкой средой при ультразвуковой мойке являются органические растворители (бензин, спирт, смесь бензина со спиртом — для очистки от жировых и механических загрязнений; ацетон или ацетон со спиртом — для очистки деталей от смол и нитроэмалей), а также водные растворы щелочей и синтетических поверхностно-активных веществ. При очень тщательной мойке применяют жидкий фреон. Некоторые конструкции ультразвуковых установок имеют устройства для автоматического переворачивания деталей в процессе очистки. Температура органических растворителей поддерживается не более 30 °С, водных растворов 45. . .60 °С. Степень очистки до 0,4 г/м 3 . В зависимости от требований к уровню очистки моющий раствор подвергается той или иной степени фильтрации.
В наиболее ответственных случаях устанавливаются нормативы остаточной загрязненности деталей после мойки.
16. Подъемно-транспортное оборудование сборочных цехов
Кроме основного оборудования, в сборочных цехах широко применяется вспомогательное подъемно-транспортное оборудование:
- гидравлические, пневматические и пневмогидравлические домкраты;
- электрические лебедки, полиспасты и тали;
- электро- и пневмоподъемники;
- специальные подъемные устройства.
Подъемно-транспортные операции выполняют с помощью:
- тельферов;
- кран-балок;
- мостовых и козловых кранов;
- поворотных кранов;
- напольных передвижных кранов.
Транспортные работы осуществляют с помощью:
- рольгангов;
- рельсовых и безрельсовых тележек;
- конвейеров.
Нужное вспомогательное оборудование для сборочных работ выбирается в зависимости от типа (масштаба) производства, вида организации процесса сборки, конструктивных и технологических особенностей собираемых изделий.
Рис. 31. Элементы рольганга: 1 — откидная секция; 2 — поворот рольганга; 3 — поворотная секция; 4 — подводящий рольганг.
Рольганги, называемые еще роликовыми конвейерами, применяемые на сборочных участках, могут иметь привод, а могут быть без привода. Для крупных сборочных единиц ролики рольгангов располагают на уровне пола, для средних и малых — на высоте рабочей поверхности верстака (от 0,6 до 0,8 м) . Конструкции рольгангов позволяют изменять направление сборочного потока (рис. 31) . Для прохода и проезда в рольганге делается откидывающаяся секция. Узловые сборочные потоки примыкают к основной ветви рольганга. Диаметры роликов выбираются в зависимости от нужной грузоподъемности, длина — от 0,2 до 1,2 м, а в металлургии — до 5 м. Протяженность рольгангов достигает десятков метров.
При поточной сборке собираемые изделия часто закрепляют на тележках, которые последовательно передают от одного рабочего места к другому Колеса тележек могут иметь литые резиновые шины, вследствие чего их можно перемещать по обычному полу.
При значительном весе изделий тележки с металлическими колесами движутся по рельсам. Такие тележки оборудуются тормозом. Неудобство использования рельсовых тележек состоит в необходимости организации трассы для их возврата в начало потока.
При сборке малогабаритных изделий пути для движения тележек могут располагаться на высоте 0,7. . . 0,8 м. В этом случае холостые пути удобно располагать под рабочей веткой.
Транспортные конвейеры делятся на сборочные — для перемещения собираемых изделий и сугубо транспортные, подающие на сборку комплектующие.
В 1882 г. конвейер был использован для связи технологических агрегатов в поточно-массовом производстве (США). Несколько позднее стали применяться напольные (1890 г. , США), подвесные (1894 г. , Великобритания) и специальные сборочные конвейеры (1912-1914 гг. , США).
При сборке небольших изделий применяют сборочные конвейеры из прорезиненной ленты шириной 200. . .800 мм. Рабочая часть ленты скользит по гладкому столу, а холостая ветвь поддерживается роликами. На концах такого конвейера расположены ролики — приводной и натяжной Приводной механизм состоит из червячного редуктора или редуктора в сочетании с зубчатой или цепной передачей. Изделия собирают на приставленных к конвейеру вдоль или поперек его движения верстаках, а с помощью ленты передают от одного рабочего места к другому. В тех же условиях применяют горизонтально замкнутые толкающие конвейеры с программным устройством для обеспечения заданного темпа работы и автоматического адресования объектов сборки по рабочим местам.
Широкое распространение имеют приводные тележечные конвейеры (рис. 32) . Они представляют собой механизм для периодического или непрерывного движения скрепленных одной или двумя цепями тележек. Периодическое движение задается с помощью реле времени или вручную. Такой конвейер может быть вертикально или горизонтально замкнутым. Обратное транспортирование тележек по первому варианту удобнее и не занимает производственную площадь.
Рис. 32. Конвейер для сборки телескопических амортизаторов (МАЗ)
Сборочный конвейер состоит из следующих частей:
- приводной, включающей электродвигатель, редуктор или вариатор скоростей;
- тяговой (одна или две шарнирные цепи);
- несущей (ряд тележек, соединенных с тяговыми цепями);
- опорной (направляющие, по которым катятся ролики тележек);
- натяжной (для создания нормального натяжения тяговых цепей)
Если поверхность тележки закрыть листом металла или пластмассы, то получится пластинчатый конвейер. Горизонтально замкнутые пластинчатые конвейеры имеют серповидную форму пластин. Такие конвейеры применяют на обрабатывающих центрах для подачи заготовок.
Расположение конвейера определяется количеством сборочных операций и его длиной. Конвейер может быть прямым, О-образным, П-образным и т. д. Повороты конвейера на углах обеспечивают поворотные секции, аналогичные показанной на рис. 31, позиция 3.
При небольшом количестве сборочных операций применяют круглый вращающийся стол — карусельный конвейер, вокруг которого расположены рабочие места. Внутри корпуса стола помещается привод.
Для сборки крупных объектов, например автомобилей, применяют цепные напольные конвейеры (рис 7 33) Как видно на фотографии, изделия собирают на одной тележке, ролики которой опираются на рельсы, вмонтированные в пол Тележки при помощи сцепок присоединяют к тяговой цепи, расположенной в лотке ниже уровня пола. Возврат освободившихся тележек осуществляется по параллельному пути. Конвейер для автомобилей имеет тележки только на том участке, где монтируют ходовую часть Дальше собираемый объект присоединяют непосредственно к цепи Конвейер может двигаться непрерывно или периодически со скоростью 4. . . 5 м/мин с остановками, продолжительность которых равна темпу сборки.
Рис. 33. Цех сборки 40-тонных самосвалов (БелАЗ)
Приводы конвейеров в большинстве случаев электрические. Однако есть ряд конструкций, в которых использован гидравлический поршневой привод.
Если в процессе сборки требуется точное позиционирование изделий, то их собирают на шагающих (рамных) конвейерах.
Подвесные конвейеры широко применяются при сборке изделий средних размеров. На таких сборочных конвейерах обеспечены удобный подход к объекту сборки и рациональная ориентация изделия. Подвесные сборочные конвейеры могут иметь жесткую связь тягового органа с подвеской или гибкую — с помощью поводка. Вторая схема дает возможность кратковременно приостанавливать подвеску с объектом сборки для выполнения операции и позволяет автоматически адресовать собираемые объекты на другие аналогичные конвейеры.
Конвейер (рис. 34) состоит из замкнутого в пространстве подвесного однорельсового пути (фрагмент а), ходовых кареток (фрагмент б) с грузовыми подвесками (крючьями, захватами, площадками (фрагмент в) и пр. ), натяжного устройства и тягового органа (цепи, реже стального каната), скрепленного с тележками и приводимого в движение одним или несколькими приводными устройствами. Подвесные конвейеры широко применяют для транспортирования готовых изделий на испытательные станции или в окраску. Путь подвесного конвейера обычно выполняется в виде монорельса, прикрепленного к строительным конструкциям.
В отдельных производствах получают распространение сборочные конвейеры с гидростатическими направляющими и на воздушных подушках.
Рис. 34. Подвесной конвейер: а — монорельс с каретками и приводной цепью; б — двухроликовая каретка; в — схема подвеса рабочей площадки.
Рис. 35. Поворотный передвижной стенд для сборки двигателя
Машины и крупные сборочные единицы часто собирают на станках-стендах (рис. 35) . Стенды делают с неподвижными или подвижными основаниями. Изделие в стенде можно поворачивать в удобное для сборки положение.
Оборудованием для выполнения вспомогательных (транспортировка) и основных (например, сварка) автоматизированных процессов сборки как в массовом, так и в серийном производстве являются промышленные роботы.
Серийность производства определяет технологию и конфигурацию сборочной системы. Для автоматических сборочных линий в условиях массового производства, как правило, применяются однооперационные сборочные модули на основе ПР. В условиях серийного производства чаще используют многооперационные сборочные модули и операция сборки производится в специальном приспособлении с помощью одного или нескольких ПР.
Технологическое оборудование — это что такое?
Для производства любых товаров (за исключением интеллектуального труда) требуются специальные механизмы. Иначе – технологическое оборудование. Это могут быть станки для обработки металлов резанием, кузнечно-прессовое оборудование, литейные, ткацкие и другие виды станков, а также оборудование для пищевой, химической, фармацевтической и других видов промышленности. Перечень можно продлить до бесконечности. Технологическое оборудование предприятия определяет его конкурентоспособность и востребованность производимой продукции.
Общие понятия
Исходное сырье и материалы загружаются и подвергаются обработке на оборудовании технологического процесса. После завершения определенной операции материал либо заготовка претерпевают существенные изменения. Так, например, при загрузке стальных изделий в печь, дальнейшего нагрева их до критических температур и охлаждения свойства материала изменяются скачкообразно. В качестве среды охлаждения может выступать воздух, промышленное масло, вода (как в чистом виде, так и с разнообразными присадками) и даже легкоплавкий металл. В зависимости от преследуемых целей, потребуется наличие конкретного технологического оборудования. Это зачастую дорогая импортная техника. С техническим обслуживанием такого оборудования едва ли сможет справиться слесарь без специальной подготовки.
Классификация оборудования
Прежде всего все станки, аппараты и механизмы, которые принимают участие в технологическом процессе производства изделий, классифицируют по характеру влияния на сырье (заготовку). Еще одним важным параметром является структура цикла изготовления изделий. Кроме того, оборудование можно классифицировать по производительности (количеству выполняемых операций в единицу времени), по назначению и по степени автоматизации и механизации.
Авторы различных учебных пособий придерживаются разных методологий при классификации технологического оборудования. Это создает определенные трудности для самостоятельного изучения ряда инженерных дисциплин. Особым разнообразием подходов характеризуются зарубежные учебники. В условиях России рекомендуется брать за основу приведенный перечень.
Классификация по степени автоматизации
По данному критерию технологическое оборудование делят на механизмы с ручным управлением, полуавтоматы и автоматы.
Следует сказать, что оборудование с ручным управлением постепенно исчезает из обихода. В соответствии с современными представлениями, человек не должен выполнять физически тяжелую работу, которую могут выполнять роботы. Однако в некоторых случаях универсальные станки применяются. Причем в ближайшей перспективе они не будут вытеснены автоматикой. Это, прежде всего, касается ремонтных мастерских, которые занимаются вспомогательным обслуживанием производств.
Воздействие на обрабатываемое сырье или заготовку
По данному признаку принято все машины и аппараты делить на две большие группы. Это технологическое оборудование, которое в процессе обработки меняет геометрию (размеры, формы) заготовки. Ко второй же группе относятся машины, которые при воздействии на сырье и материалы изменяют их физические и химические свойства.
Примерами технологического оборудования первого вида могут служить токарные, фрезерные и другие металлообрабатывающие станки, а также оборудование литейной группы, машины для горячей и холодной ковки металла и т.д.
Вторая группа – это промышленные печи для термообработки металлов и сплавов, оборудование для варки сахара и другие аналогичные аппараты.
Следует отметить, что у оборудования первой группы, как правило, гораздо больше движущихся частей. К тому же оно испытывает значительные нагрузки. Поэтому ремонт технологического оборудования данного класса осуществляется гораздо более часто. Машины, которые не участвуют в формообразовании поверхностей изделий, работают стабильно и выходят из строя крайне редко. Так, например, промышленные печи чаще всего выходят из строя по причине перегорания нагревателей.
Встречаются редкие высокотехнологичные экземпляры оборудования, которые представляют собой машины универсального типа, способные обрабатывать изделия и придавать ему заданную форму и свойства. Такое оборудование может быть отнесено одновременно как к первому, так и ко второму виду.
Классификация оборудования по структуре цикла
Цикл процесса обработки – это не что иное, как время от начала загрузки исходного сырья или установки заготовки до завершения процесса обработки и отправки предметов труда на склад либо на следующую операцию.
Машины бывают периодического и непрерывного действия. Как те, так и другие обладают своими преимуществами и недостатками, которые отражаются на экономических показателях деятельности предприятия.
Оборудование периодического действия
В первом случае заготовка (сырье) обрабатывается машиной в течение определенного времени, после чего она снимается с приспособления и отправляется на дальнейшие операции, а машина обрабатывает очередное изделие (порцию сырья). Примером таких машин служат металлообрабатывающие станки, доменные печи, промышленные мясорубки и другие. Такие машины относятся к основному технологическому оборудованию. Хотя и из этого правила есть исключения.
Эксплуатация технологического оборудования периодического действия требует от исполнителя работ специальной подготовки и навыков. В противном случае такие машины будут постоянно выходить из строя.
Оборудование непрерывного действия
Отличительная особенность таких машин – одновременная выгрузка готового сырья (изделий) и поступление полуфабрикатов (установка заготовок) в машину. Таким образом, организован непрерывный цикл производства. Технологическое оборудование работает в режиме нон-стоп. Отсутствие технологических перерывов негативно сказывается на работе оборудования. С течением времени случаи выхода его из строя учащаются.
Примером машины непрерывного действия является автомат по производству изделий из полиэтилена: на вход поступают гранулы пластика, при этом постоянно выходит и наматывается на бобину полиэтиленовая лента. Также к такому оборудованию относятся автоматы роторного типа.
Преимущество от использования такого оборудования заключается в его просто невероятной производительности. Она подчас превышает производительность традиционных машин прерывного цикла в несколько десятков раз.
Классификация по количеству выполняемых операций
По данному признаку все оборудование можно поделить на многооперационное и однооперационное.
Каждый из двух типов имеет свои показания к применению для разных видов производств, а также достоинства с недостатками. Не всегда более дорогое оборудование будет выполнять свою работу лучше, чем гораздо более дешевые отечественные аналоги.
Однооперационные машины
Из названия понятно, что к данному классу технологического оборудования относят машины и механизмы, которым отведена задача выполнять лишь одну технологическую операцию.
Примерами такого технологического оборудования могут служить ленточные пилы. Данный станок может выполнять сугубо одну функцию – нарезку проката на заготовки разной длины. Примеры из другой отрасли промышленности – мясорубка в мясоперерабатывающем цеху мясокомбината, аппарат для нарезания хлеба на ровные куски и т.д.
Многооперационные машины
На таком оборудовании может выполняться огромное количество операций. Оно считается универсальным.
Возможность осуществления выпуска большой номенклатуры изделий весьма привлекательна. Однако в массовом и крупносерийном производстве такие машины применять крайне нежелательно по причине их «капризности». Такое оборудование является очень высокотехнологичным, поэтому за ним требуется тщательный уход и техническое обслуживание. В условиях массового производства этим мерам предупреждения поломок, откровенно говоря, не уделяется внимания вообще. Как правило, станки и механизмы ремонтируются по требованию (при возникновении поломок и выходе из строя). Ведь основное технологическое оборудование часто работает в три смены, а порой и семь дней в неделю. Поэтому оно должно быть надежным. Для таких целей используют специальное оборудование. Да, его технологические возможности ограничены, но и конструкция таких станков максимально упрощена, а значит они работают надежно и без поломок. Необходимо лишь следить за уровнем масла в коробке передач и за подачей охлаждающей жидкости в зону резания.
При таких условиях большинство высокотехнологичных решений окажутся невостребованными и будут лишь мешать.
Технологическое оборудование
Технологическое оборудование для предприятия представляет собой агрегаты и устройства, которые выполняют часть технологического процесса производства продукции или полный цикл изготовления продукции.
Благодаря их наличию все процессы производства или основная их часть выполняется в автоматическом режиме, позволяя, при этом, сокращать использование рабочей силы, ускорить процесс изготовления и усовершенствовать технологию производства. Технологическое оборудование для предприятия классифицируется на основании таких показателей, как функции оборудования и отрасль его использования.
Наша продукция:
Кондитерское оборудование;
включает в себя
- Планетарные миксеры.
- Машины для формирования мучных кондитерских изделий: отсадочные машины, экструдеры, вафельницы, тарталетницы, машины для формовки сухарных плит, машины для формирования бараночных изделий и др.
- Кремонаполнители.
- Глазировочные машины.
- Измельчители продуктов (пудромолки, измельчители шоколада, овощерезки).
- Заварочные машины.
- Кремоварки.
- Темперирующие машины.
- Машины для отливки мармелада.
- Дозаторы начинок.
- Машины для декорирования.
- Кондитерские формы, тележки, листы.
- Машины для расфасовки и упаковки.
- Охлаждающий туннель.
Оборудование для кондитерского производства может быть как в виде отдельных автоматов, блоков, различных модульных систем, так и целыми линиями.
Спроектируем ваше новое производство, подберем комплекс оборудования или модернизируем существующее, с заменой узлов и агрегатов.
Мясоперерабатывающее оборудование;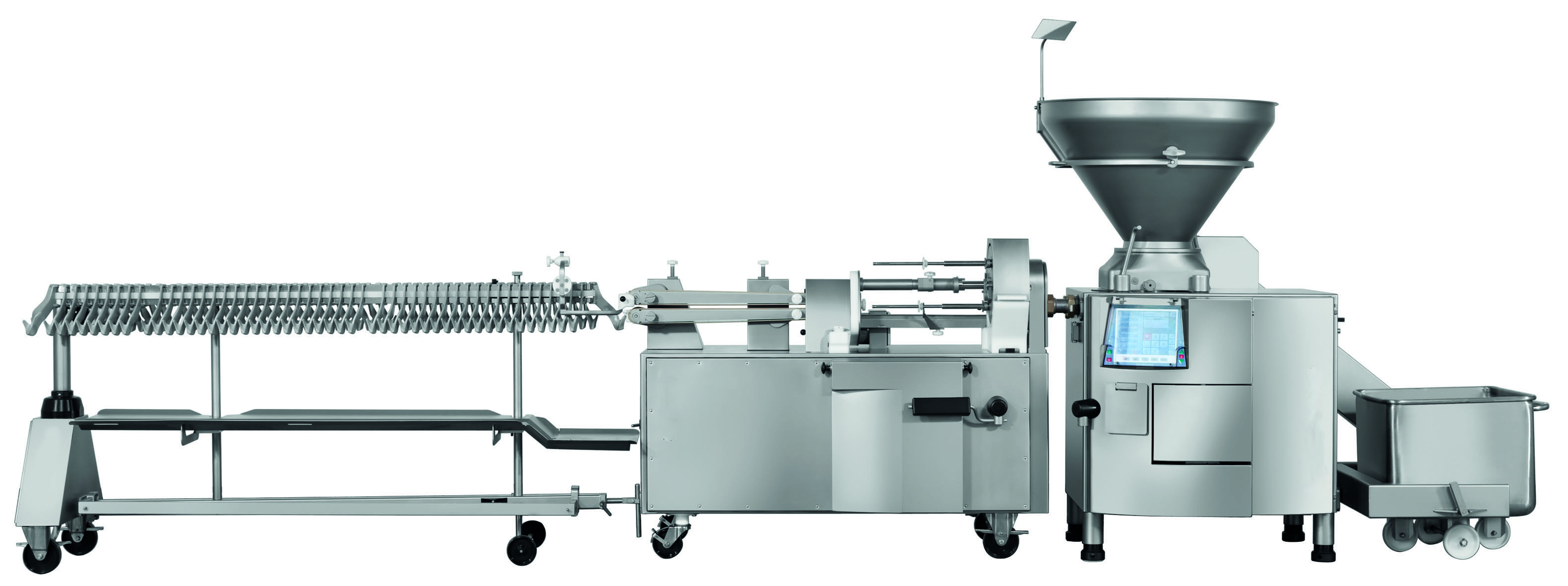
- Термокамеры — универсальные, для запекания, жарки, варки и копчения, позволяют уменьшить время приготовления мясных и рыбных изделий, сделать процесс приготовления полностью автоматическим. Производятся в различных вариациях: одно, двух или трехрамных конструкциях.
- Мясомассажеры. Эти устройства ускоряют процесс засола мяса в разряженной емкости, что улучшает потребительские свойства и увеличивает выход готовой продукции.
- Фаршемешалки разработаны с применением передовых технологий. Используются для изготовления мясного фарша при производстве всех видов колбас, а также при выпуске мясных хлебов, ветчин. На модели объемом 335 л и 630 л можно установить вакуумную станцию и тепловую рубашку.
- Столы технологические разнообразных видов и размеров.
- Тележки емкостью в 100, 200, 500 л. Применяются для загрузки и перемещения продукции. Преимущество тележек — надежность и простота конструкции, которая позволяет служить длительное время.
- Рамы колбасные. Используются для размещения рыбы, птицы, колбас, мясопродуктов при их термообработке в термокамерах и транспортировке.
Хлебопекарное оборудование;
Основные виды оборудования для хлебопекарного производства:
• Оборудование загрузки, транспортировки и разгрузки сыпучих компонентов и муки.
• Дозаторы муки, воды.
• Тестомесы ( тестомесильные машины)
• Тестозакатывающая машина и тестораскаточная машина.
• Тестоделительные машины
• Округлитель теста ( тестоокруглительная машина).
• Расстоечные шкафы.
• Хлебопекарные печи. Хлебопекарные ротационные печи.
• Хлеборезательные машины. Слайсеры.
• Формы для выпечки хлеба и для расстойки.
• Тефлонированные, чугунные и алюминиевые формы для хлеба.
• Нейтральное оборудование. Столы и тележки для хлеба.
• Конвейеры и транспортные системы.
Молокоперерабатывающее оборудование;
включает в себя ванны длительной пастеризации, ванные охлаждения, пастеризаторы, гомогенизаторы, парафинеры, различные охладители, насосы, анализаторы молока, фильтры, автоматы розлива, линии производства сыра и масла и другое.
Для хранения молока обычно используют емкостное оборудование с охладителем или нагревателем или без него, в зависимости от требуемых условий хранения. Оно бывает вертикальное и горизонтальное, различной формы – цилиндрическое, прямоугольное, корытообразное. Для молока, сливок и других жидких молочных продуктов с недолговременным сроком годности используют приемные баки, ванны.
Для транспортировки на дальние расстояния и приемки молочной продукции пользуются транспортными специальными цистернами и емкостями технологического назначения.
Для транспортировки внутри предприятий используют молокопроводы, насосы различного типа и транспортные системы. Способ перемещения сырья на молочное производство значительно влияет на себестоимость получаемой продукции и его качество. Важно соблюдать неизменность структуры и свойств самого продукта, исключением являются емкости, в которых эти изменения создаются.
К видам оборудования для механической и тепловой обработки молока относятся фильтры для первичной очистки молока, удаления биологических загрязнений, сепараторы для разделения цельного молока на две составляющие – сливки и обезжиренное молоко.
К оборудованию для выработки молока относят гомогенизаторы для производства питьевого молока и подготовке к производству кисломолочных напитков и сывороток, сметаны, творога, сгущенного молока, сливочного масла и других молочных продуктов, диспергаторы для изготовления молочных продуктов из составного сырья (например, молоко сухое, растительные жиры, другие составляющие), а также нагреватели, охладители и приборы для термовакуумной обработки.
Каждый представленный агрегат – это современное надежное устройство, которое изготавливается из прочных, износостойких материалов, сертифицировано и отвечает европейским стандартам качества.
На все оборудование предоставляется гарантия от 1 года до 5 лет.Реализовывая технологическое оборудование для предприятия, мы предоставляем своим клиентам не только услугу гарантийного обслуживания, но и готовы выполнить ремонт технологического оборудования любой сложности.В наличии имеются оригинальные запасные детали от завода изготовителя, которые обеспечат вам дальнейшую бесперебойную работу агрегатов.
Преимущества использования технологического оборудования:
производственный процесс изготовления той или иной продукции включает в себя несколько циклов, автоматизация которых, за счет использования технологического оборудования для предприятия, предоставит вам следующие преимущества:
-
- Увеличение объемов производства;
- Четкое разграничение количества ингредиентов и составляющих, и контроль их использования;
- Сокращение количества обслуживающего персонала;
- Получение высококачественного продукта;
- Товарный вид изделий.
Европактрейд — поставка технологического оборудования
Адреса: г. Воронеж, ул. Бульвар Победы, дом 50в, офис 15
г. Москва, ул. Остаповский проезд, д. 5, оф. 405
Телефоны: +7 (495) 782-92-32 МОСКВА, +7 (473) 262-15-60 ВОРОНЕЖ; 8-800-500-00-14 БЕСПЛАТНОМы работаем в Москве, Санкт-Петербурге, Новосибирске, Екатеринбурге, Нижнем Новгороде, Самаре, Омске, Казани, Челябинске, Ростове-на-Дону и других городах России.
Источник https://extxe.com/3658/tehnologicheskoe-oborudovanie-dlja-sborki/
Источник https://businessman.ru/tehnologicheskoe-oborudovanie—eto-chto-takoe.html
Источник https://euro-pack.ru/articles/texnologicheskoe-oborudovanie